$59+ SHIPS FREE! (USA)
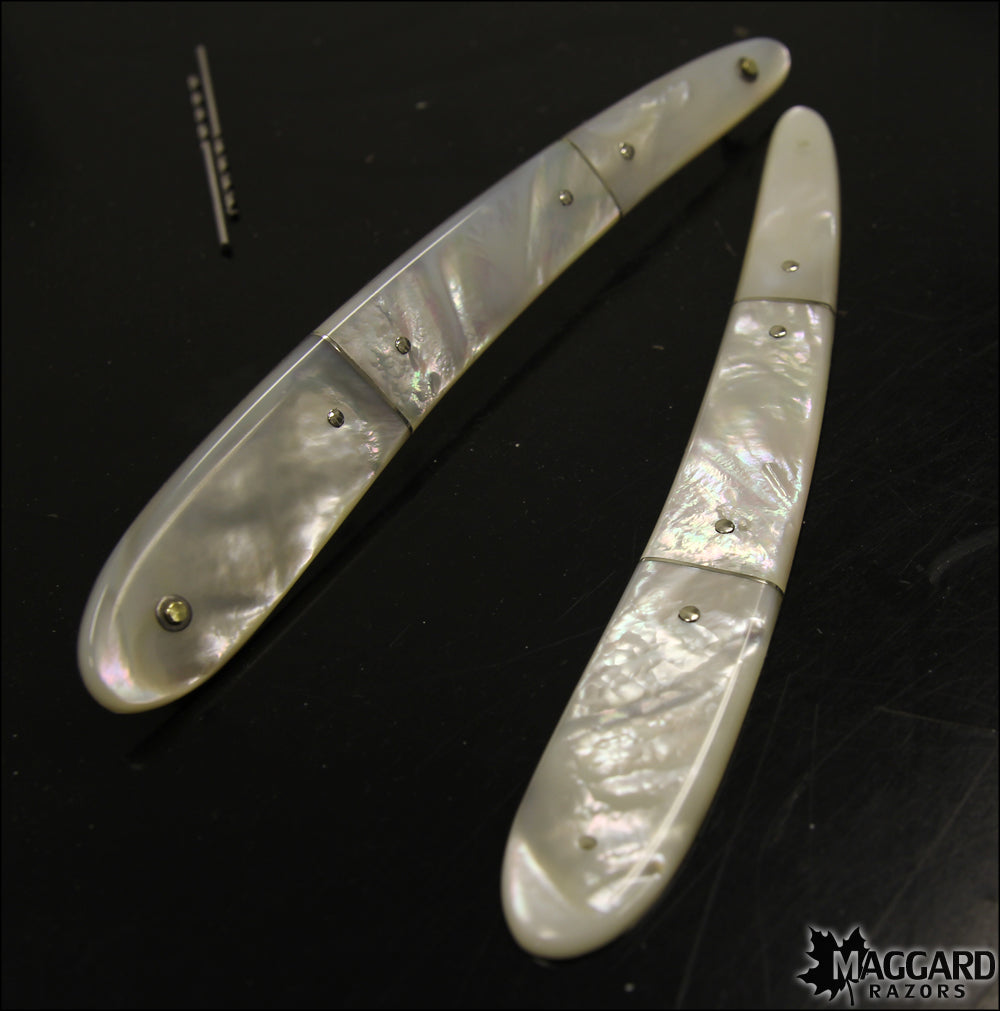
Custom Straight Razor Mother of Pearl Scales - Making Of (Part 2)
This post is a continuation of my Custom Straight Razor Mother of Pearl Scales - Making Of (Part 1)
Update!
So, I took the scales off of the clamps, and then I scraped off all of the paper that was super glued on the nickel sheeting. Then, I took my 1/16" Drill bit and drilled right through all of the holes that were in the nickel sheeting straight through the 3 MOP panels on the other side. This made it so that the holes were perfectly positioned. Obviously I have quite a bit of excess MOP material hanging off the sides. that is OK though! :)
Then, I sanded the MOP side flat with my disc sander. This ground down the excess nickel sheeting that was sticking out on the panel dividers.
I was then able to do the whole thing over again on the other side. I trimmed up the MOP pieces to the correct dimensions, and then epoxied them in place, starting with the center piece:
And then I put in my nickel panel dividers and epoxied in the other two panels:
You can see the dividers sticking out. All that excess material will go away after it sets up!
After it set up, I unclamped the scales. The epoxy set extremely solid.
I took it to the belt sander, and flattened out the pile side scale
After that, I used the pre-drilled holes on the front scale to drill through the pile side scale.
I then did some more profiling with the belt sander, and when I started getting close to my original tracings, I took the original scale and I bolted it on to the the MOP scales so that I had an exact profile to match.
You can see a little bit of excess material that I had to grind down.
After a little more sanding, I was close to the original profile
You can see no overhangs now :)
Then, I spent about 30 minutes on the belt sander, very carefully and slowly thinning out the scales (they started around .125" ea, and I thinned them to approx .11"). MOP chips easily, and sands slowly, so, it was a delicate process.
So, it was on to hand sanding. I started at 220 grit and went to town.
With every grit, it got prettier and prettier
After a buff, I was just stunned!
Unfortunately, there was no time to enjoy. it was on to the next step. I started to carefully pin the panels on to the nickel liners, one hole at a time
After each of them were pinned, I buffed up the heads on the MOP side
Then I ran some 1000 grit sandpaper along the back side of the scales (the nickel sheeting, and then gave them a quick buff. A final buff will come later.
Here is another shot, ready for pinning.
I decided to use the original lead wedge, but, it was pretty gunky, so, I started to clean it up
Here are the edges, polished up
Then it was just a matter of pinning it into the wedge end of the scales
And finally, here it is - the reason for ALL of that work - a mother of pearl scale that is capable of flexing!
And finally, the results!
Check out the Full Gallery!


























Comments
Leave a comment